About Us
Why Copperhead Press?
Our name draws its inspiration from the biblical account in Numbers 21:9. The Israelites were struck by a plague, and God told Moses to make a copper serpent. Anyone who looked at it was spared.
In the same spirit, we see classic, time-tested literature as a kind of safeguard—works whose enduring relevance lies in their ability to convey profound truths across generations. Whenever we open them, they help guard us from the “plague” of ignorance that can so easily creep in. They give us wisdom, perspective, and a way to see the world more clearly—no matter when or where we’re reading them.

ABout us
Chaz & Katie Ross
We are a husband-and-wife team dedicated to the art of handcrafting books. Every edition we produce is made entirely by hand—from handsewn signatures to our own paste papers, custom slipcases, and clamshell boxes. Our mission is to bring classic works of literature from our bindery to your personal library.
Scroll below for a closer look at our process:

design process
Formatting
One of the earliest steps in our process is transforming the raw text into a carefully considered digital layout. This stage involves a series of important design decisions: selecting the typeface, determining the inclusion of images, composing a foreword, and defining the dimensions of the text block. We also paginate the content into 12- or 16-page signatures to ensure structural integrity and minimize blank pages at the end of the book. At this stage, we also finalize the limitation page—meaning the overall design, materials, and edition details must be confirmed and committed.

design process
Outward Design
As we mentioned, the limitation page for each edition is locked in before the files go to the printer. That page lays out all the key details for that specific version, so a lot of design choices have to be made early on. Just picking the leather involves a bunch of decisions—what color, what kind of hide, where we can get it from, how long it takes to arrive, and which supplier offers the best quality. And that’s only the start. We also have to choose everything else carefully: the endpapers, headbands, the paper for the text block, the book board, plus how the slipcases and clamshell boxes are built. Every piece has to come together perfectly. It’s really a kind of quiet dance between materials, vision, and care.

binding process
Preparing Signatures
Once the printed signatures arrive from the press, the binding process can finally begin—a welcome shift after the long stretch of design and digital layout. Each signature is folded by hand, using either fingertips or a bone folder, setting the stage for the quiet, tactile work that follows.
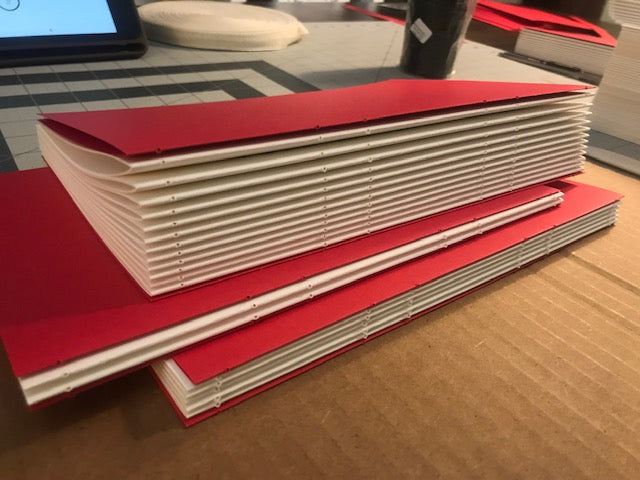
binding process
Prepping for Thread
After all the signatures are folded, we use an awl to punch sewing stations into each one by hand. These holes must be placed with precision, as their alignment determines how the signatures will come together when sewn. We follow a measured pattern to ensure consistency across the entire text block. A bit of bookbinding history: in the 1800s and earlier, all books were sewn by hand—so skillfully, in fact, that many binders could skip this step entirely, sewing each signature freehand with remarkable accuracy.

binding process
Sewing Signatures
With the holes punched, the sewing process begins. We use waxed bookbinding thread, which allows the thread to glide smoothly through the paper. It’s a technique that requires a careful hand—pull too tightly and the thread can tear through the page; too loosely, and the binding lacks integrity. When a length of thread runs short, we extend it using a specialized bookbinding knot. We prefer to tie this knot on the outside of the signature, where it remains hidden from view in the final book.
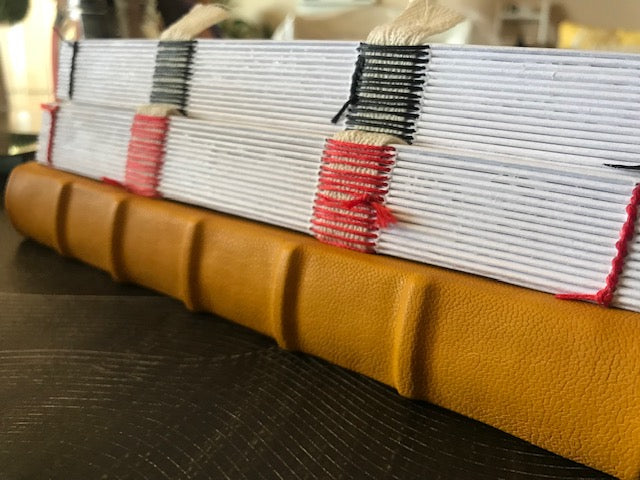
binding process
More Sewing...
Hand-sewing is one of the most time-intensive stages of the entire process—but the results are well worth the effort. A hand-sewn book opens beautifully, with a strength and durability that ensures it will last for generations. To keep our minds engaged during the long hours at the sewing frame, we often listen to audiobooks or podcasts. After a few days of steady stitching, the rhythm can become meditative—though occasionally monotonous. In the photo, you can spot the subtle knots where additional thread was joined along the way.

binding process
Sewn On Endpages
In addition to sewing the signatures, we also sew the endpapers directly onto each book. While many books—even hand-sewn ones—have endpapers simply tipped on with a line of glue, we prefer the added strength and refinement of sewn endpapers. This method reinforces the binding and, in our view, adds a subtle elegance to the finished book.
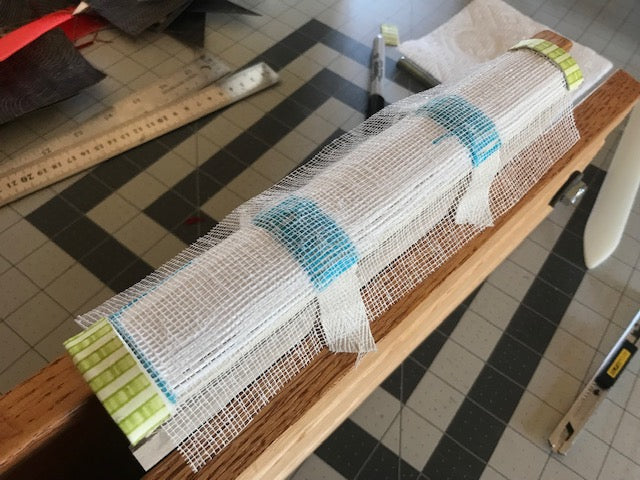
binding process
Rounding & Backing
Next, the text block is carefully rounded using a bookbinder’s hammer. While it may seem counterintuitive to treat the delicate pages so gently and then apply pressure and impact, this step is essential to shaping the spine properly. It’s a delicate balance—too much force can cause damage, but too little won’t achieve the desired result. This classic technique, part of the art of bookbinding, prepares the spine for added reinforcement. At this stage, we also add the “scrum” to stabilize the binding further, and the headbands are attached to complete the text block.

binding process
Hand Sewn Headbands
Some of our Lettered Editions feature hand-sewn headbands—a meticulous process that can take hours. This involves looping and stitching satin thread over a leather core, building the headband one thread’s width at a time until it matches the width of the text block. Once one side is complete, the book is flipped to repeat the process on the opposite end. This intricate step adds significant time to the production of each book.
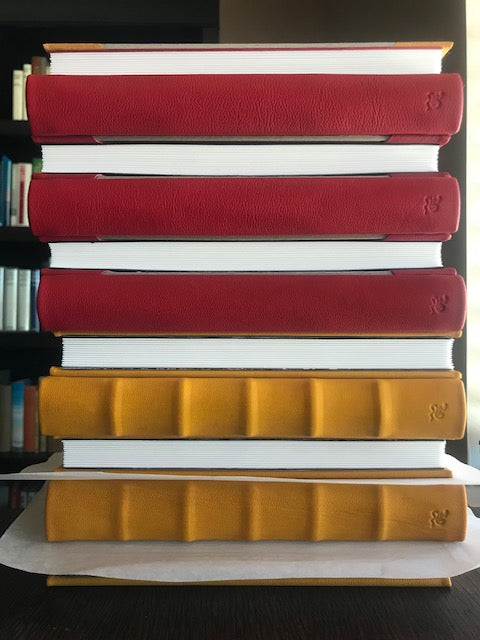
cover process
Leather Prep
At this stage, we set the text block aside temporarily to begin constructing the cover. The specific steps vary depending on the materials used. When working with leather, each panel—whether full or half—is carefully cut from goat, sheep, or calfskin and pared along the edges. This paring process, performed with a very sharp blade at a precise angle, ensures a clean, refined edge when the leather is adhered to the book board. Achieving the correct cover dimensions requires careful calculation and multiple measurements to guarantee a perfect fit. Additionally, on some editions, we emboss the spines before casing the text block into the cover, adding a final touch of craftsmanship.

cover process
Making Paste Paper
Each of our paste papers is handcrafted from start to finish. We begin by making our own wheat paste—enhanced with a touch of clove for added longevity. The paste is then mixed with paint to achieve the desired color before being carefully brushed onto the paper. Katie is the true master of this process. (At times, I wonder what my role really is…) She dedicates entire days to brushing, drying, and pressing the papers, which are spread throughout the house overnight to dry before being ready for use each morning.
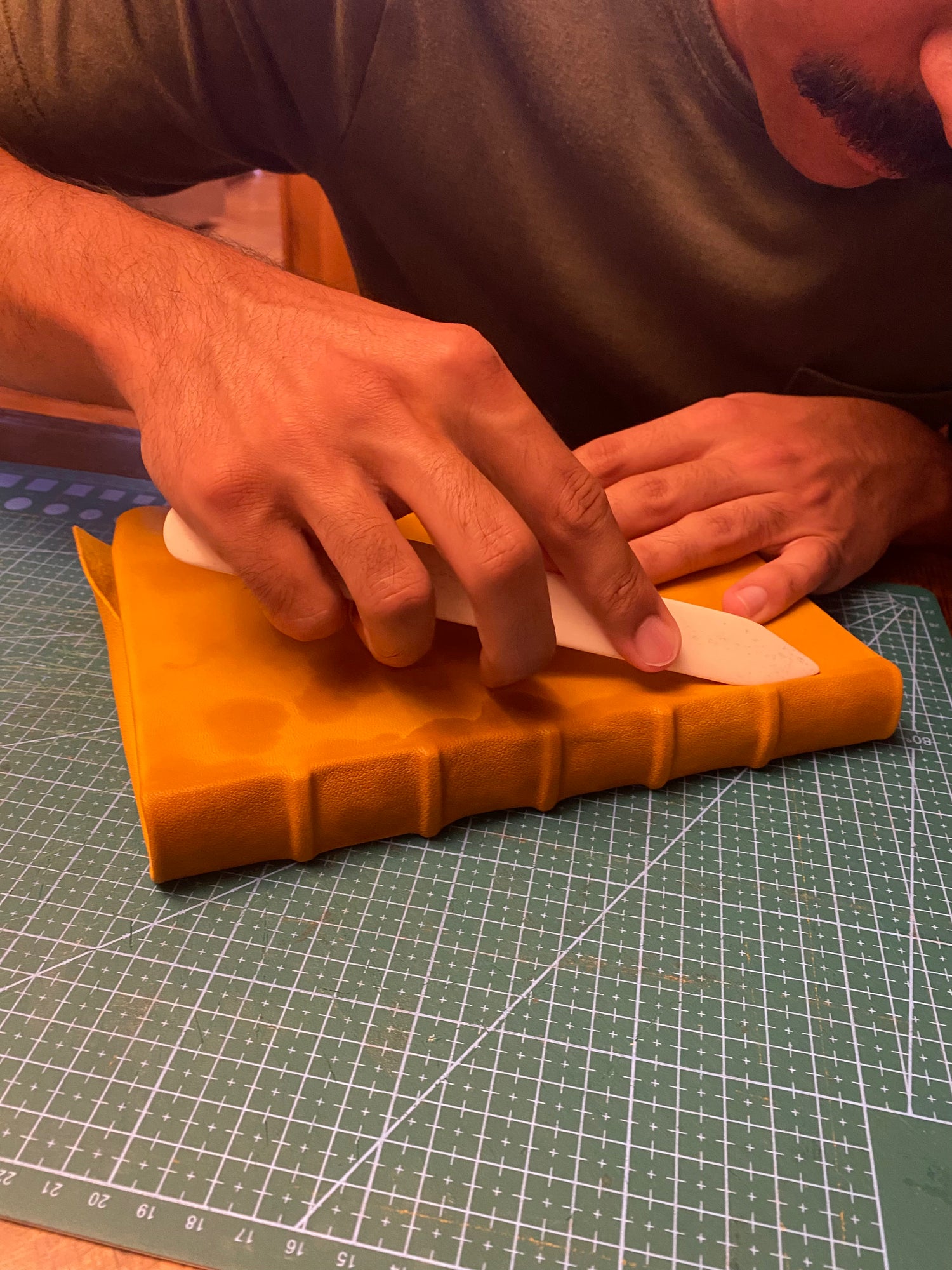
Cover process
Leather Work
Leather is honestly a joy to work with—the smell, the feel, and how it bends and moves make it something special. But it’s also tricky, because one wrong move can ruin a beautiful hide. There are lots of little tricks you have to learn before cutting into high-quality leather. One we’ve picked up is to wet the outside of the hide before putting paste on the inside. This helps both sides dry evenly and stops the paste from soaking through and leaving ugly spots. In the photo, you can see the wet patches from that step—after drying overnight, the leather looked perfect. The raised bands on the spine come from stretching goat skin over leather lace, making those classic hubs.
Bottom line: leather is the best—full of life, but you’ve got to treat it right.

cover process
Spine Labels & Casing In
There are various types of spine labels used in bookbinding. Some are printed on finely textured paper, while others are embossed onto leather tags or directly onto the book’s spine. Once the spine labels are applied, the text blocks are carefully cased into their finished covers.
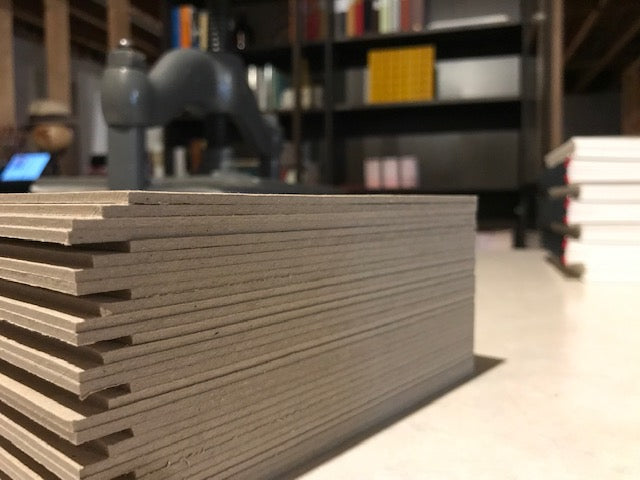
slipcase and clamshell process
Slipcase & Clamshell Production
Slipcases and clamshell boxes begin as carefully measured and cut stacks of book board, which form the sturdy structure that protects each volume. From there, the assembly becomes a precise puzzle—panels are joined, edges are wrapped with chosen materials, and the whole is reinforced to create a durable, elegant enclosure that complements the book it houses.
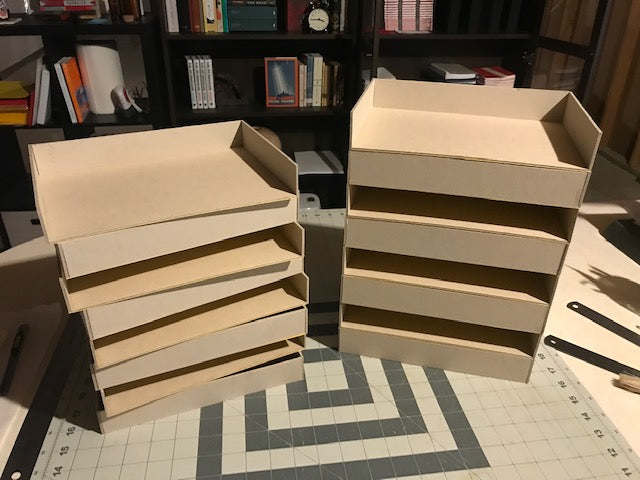
clamshell process
Building Trays
After cutting, the boards are assembled into two trays of different sizes. The smaller tray must fit precisely inside the larger one when the clamshell closes, with enough clearance between them to accommodate the thickness of the covering material. It’s definitely a bit tricky to get just right the first few times.
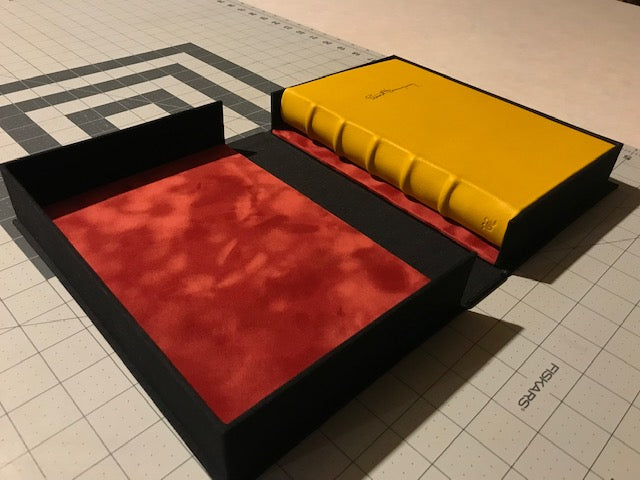
Clamshell Processing
Covering Trays
Each tray is carefully wrapped with durable book cloth around the walls, ensuring a smooth and protective finish. The bed of each tray is lined with soft, luxurious suede to provide a gentle resting place for the book. These trays are then mounted onto a rigid folio, which serves as the outer casing of the clamshell box, providing both structural support and a refined exterior. The precise alignment and secure attachment of these components are crucial to ensure the clamshell opens and closes smoothly while protecting the volume inside.
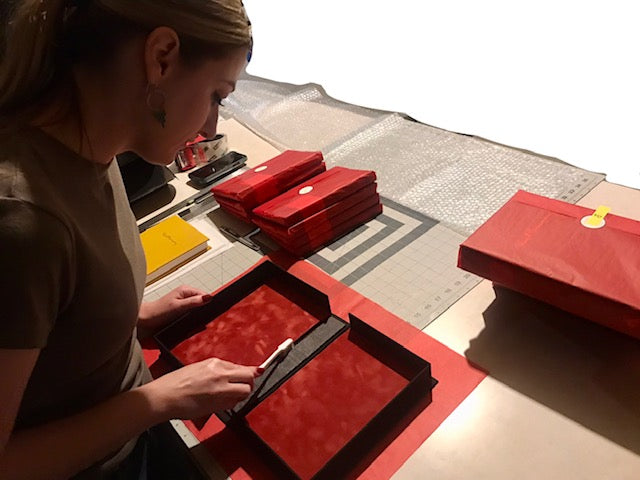
clamshell process
Finishing Touches
After putting together and gluing all the parts of the clamshell, we give everything a careful quality check to make sure it’s just right. One special touch we add is a central strip of book board — you can see Katie cleaning around it with a toothbrush in the photo. This strip acts like the fourth side of the smaller tray, fully protecting the book on all sides when the clamshell is closed. When you open it, this side folds down with the center, making it easy to take the book out while keeping it safely enclosed.

shipping
Ready to Ship
We put a lot of care into packaging our books for shipping. After all the time and effort that goes into making each one by hand, it would be heartbreaking for them to get damaged on the way to you. That’s why we wrap every book in extra bubble wrap and protective paper. For our rarest editions, we go even further and send them double-boxed to make sure they arrive safe and sound.
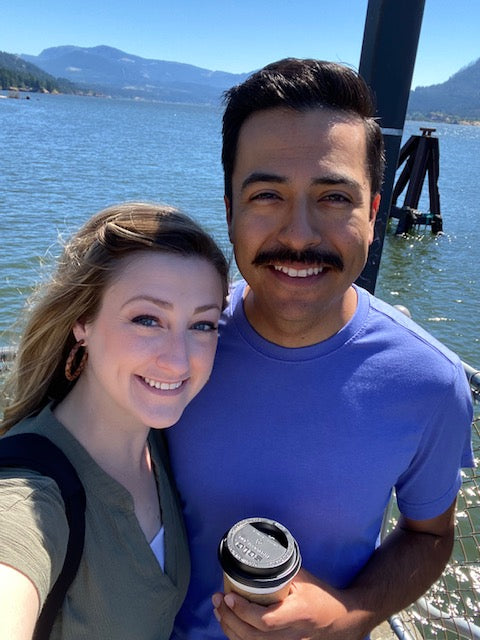
Thank You!
We’re really proud of the care and craftsmanship that goes into every book we make, and we’re so glad you took the time to learn about our process. If you decide to support our press, we can’t wait to hear what you think of your new books!
Here’s what a few of our readers have shared:
“I can't get over how beautiful they are -- such care in production and such sublime taste in the design. I will treasure them.” - Mark
“I mean, the books looked gorgeous in the photos you had sent but I wasn't really prepared for the kinds of art objects they would be in their own right. Just beautiful.” - Michael
“It was a real treat to unbox these! Even more so to hold the editions in my hands and feel and see the exquisite beauty and hard work up close. I cannot wait to spend some quiet time reading and enjoying them.” - Kevin
Multicolumn
-
Big Two-Hearted River - Lettered (Letterpress) – Copperhead Press
Experience the quiet power of nature and healing in Hemingway’s Big Two-Hearted River, a masterful journey of solitude and renewal.
-
The Sun Also Rises (Lettered Edition) – Copperhead Press
Dive into the restless spirit of the Lost Generation with Hemingway’s The Sun Also Rises, a timeless tale of love, adventure, and longing.
-
A Portrait of the Artist as a Young Man (Lettered Edition) – Copperhead Press
Follow the awakening of an artist’s soul in Joyce’s A Portrait of the Artist as a Young Man, a powerful dive into the struggles of growing up and finding one’s voice.
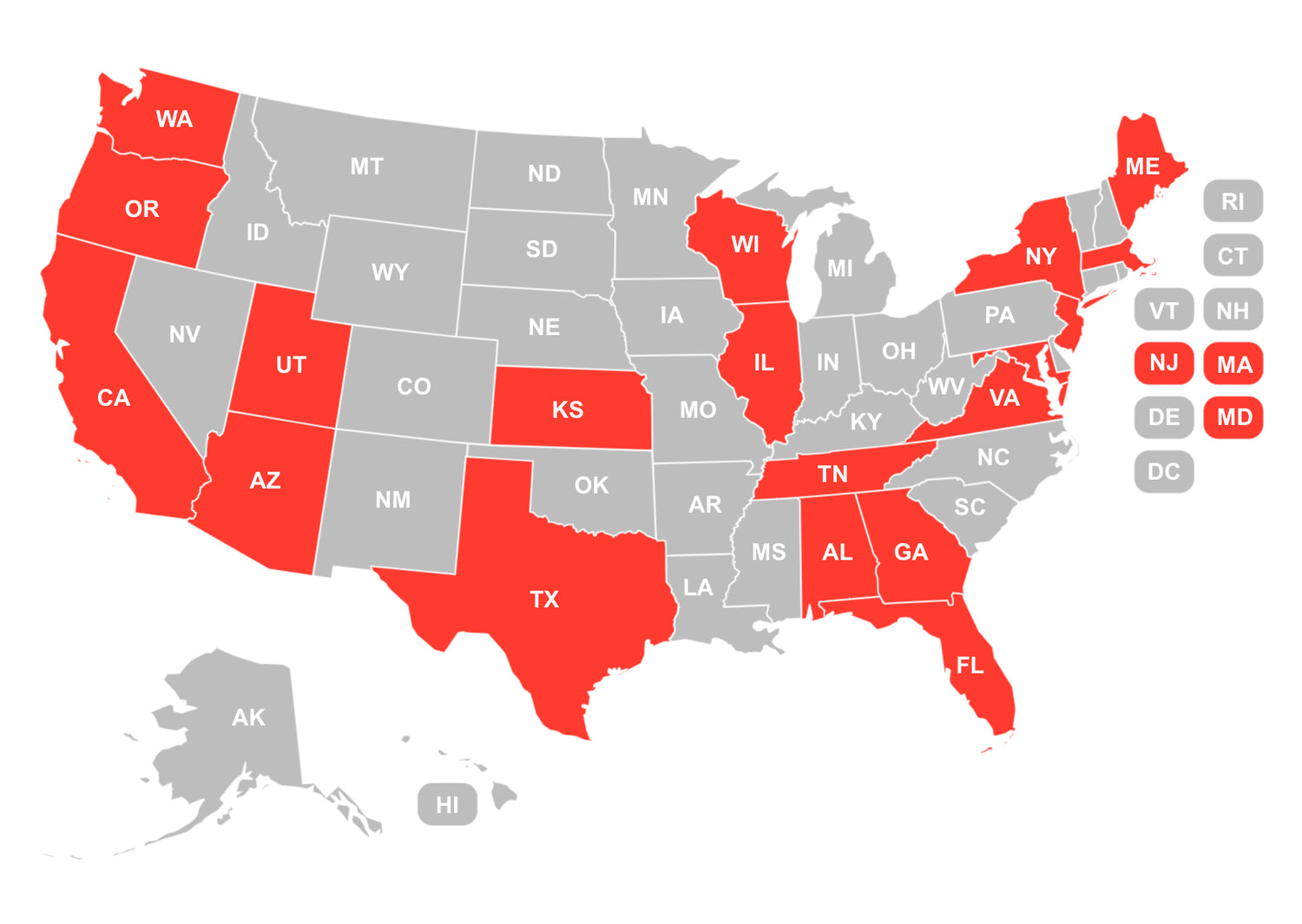
Our Domestic Footprint
In just the past year, we have already shipped or received orders from across the USA.
Nineteen states and counting! (highlighted in red)

Our International Footprint
We are also excited to see the Press gaining supporters abroad. Copies of our editions have been sent or ordered across nine countries.
Australia, Canada, France, Hong Kong (SAR), Japan, Netherlands, New Zealand, the United Kingdom & the United States.